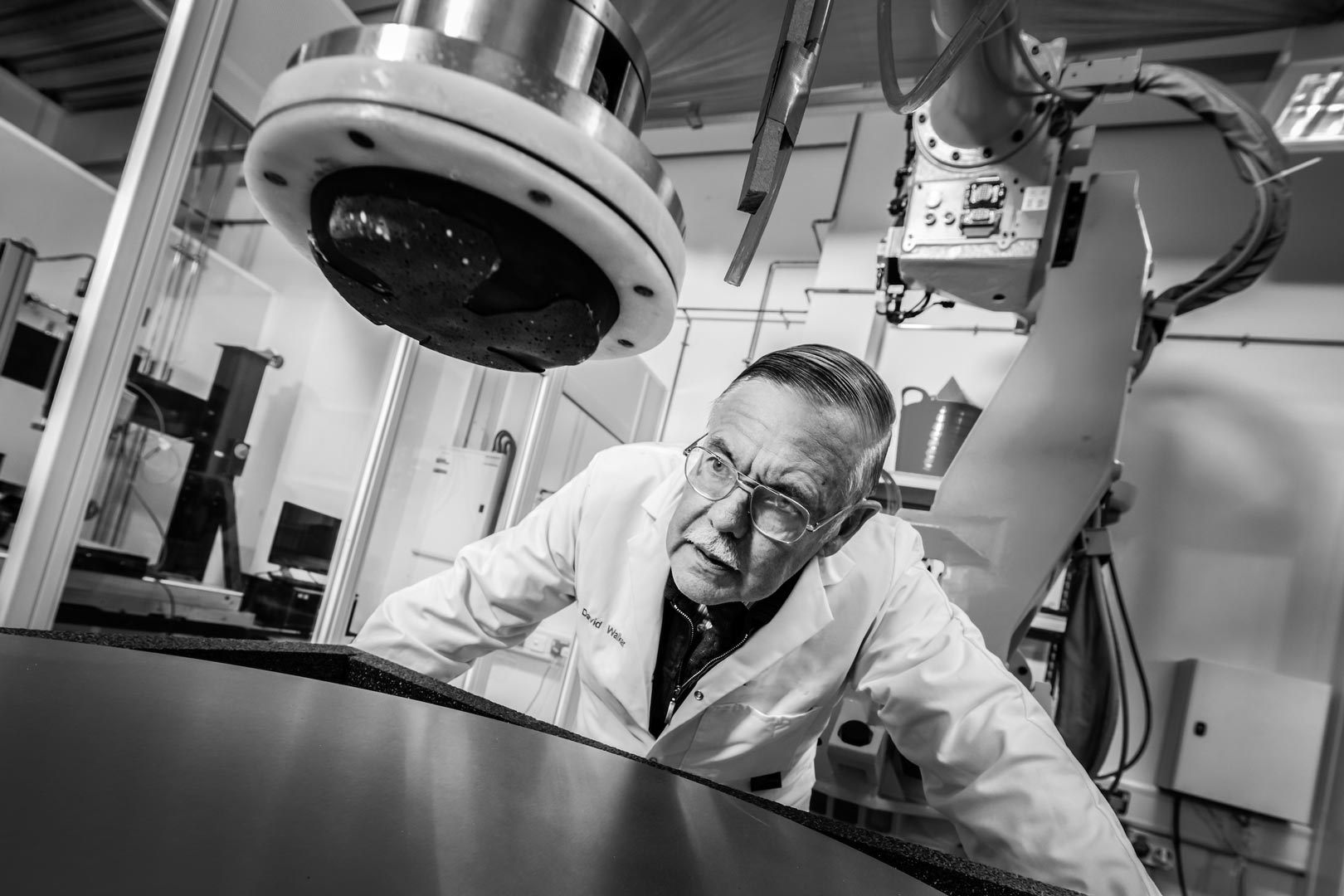
Optimised Metal Mirror Fabrication – 3 Year Project
Optimised Metal Mirror Fabrication – 3 Year Project
The University of Huddersfield laboratory for Ultra-Precision Surfaces based at SciTech Daresbury has kicked off a 3-year project- Transferring Technology in Optimised Metal Mirror Fabrication – which is funded under STFC-IPS scheme. The objective of the research project is to transfer to British Industry advanced technologies in making metal mirrors. This includes both existing methods, in which the University of Huddersfield has considerable experience, and improvements to be developed during the project. Five industry partners, Kemet international Ltd, Contour Fine Tooling Ltd, Optical Tools for Industry Ltd, Thin Metal Films Ltd and Qioptiq UK Ltd are collaborating in the project, contributing specialist expertise as well as market exploration opportunities.

The idea of making mirrors out of metal goes right back to Sir Isaac Newton's reflecting telescope, which he built in 1668 as a way to overcome the colour fringe problem with the simple glass lenses available at that time. His chosen alloy - speculum - was hard and easy to polish, but tarnished quickly, and the ability to reflect light effectively, was not good by modern standards.
Aluminium alloys have superseded Speculum, due to aluminium's availability at low cost in large sizes, and because of its superior reflection properties and durability. Whilst it expands and contracts much more than glass with changing temperature, it settles down much more quickly because it conducts heat very well. Moreover, you can drop it or shake it and it will not break!
However, aluminium has a distinct disadvantage - it is soft and difficult to polish. For this reason, aluminium mirrors have normally been made in modest sizes by turning using a very high-precision lathe and diamond tools. Unfortunately, diamond-turning inevitably leaves characteristic features on surfaces, which make the mirrors not very good for imaging in 'visible' light. Instead, they are usually used in the more-tolerant infrared (e.g. for night-vision goggles).
In metre sizes, aluminium mirrors have normally been machined traditionally, then nickel-plated, as this is easier to polish. But nickel has inferior reflection properties to aluminium, so back to square-1! Worse, the nickel expands differently from aluminium, and the whole mirror can distort with temperature changes.
With that background, the project concerns two main avenues of investigation. The first tackles removing the features on diamond-turned mirrors, using computer-controlled polishing machines and robot platforms. The diamond turning will be performed using machines on-campus, with specialised diamond tools provided by the partner CFT Ltd. Then, polishing will proceed in Huddersfield's new laboratory at the STFC-Daresbury site, using highly specialised abrasive slurries from the partner company Kemet Ltd. The technology developed will be transferred to a defence company making optics, QioptiQ Ltd.
The second avenue is to develop methods to make bare aluminium mirrors in metre sizes, as needed by partner TMF Ltd. The idea is then to position Kemet as a potential supplier, by transferring technology and so upgrading their lapping and polishing facility.
In both cases, a key aspect missing from previous research is investigating the detailed interactions between process steps. The best surface in terms of the heights of errors, may not be best for polishing, because of how those errors are distributed over the surface. We believe the project will break new ground in considering this type of approach for both avenues above.